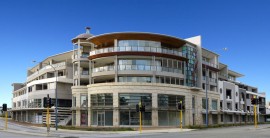
Airey Taylor Consulting was delighted to take part in the construction and design of the St Quentin’s building in the heart of Claremont.
The St Quentin’s construction concept was developed by engineers Airey Taylor Consulting as an integral part of their design solution and implemented by builders Cooper and Oxley. “A challenge for the site was achieving the maximum plot ratio whilst fronting onto one of the major traffic snarls in Perth” says ATC’s MD Peter Airey. “We addressed this by designing for top-down construction, which our engineer Basam Matty has also used in his design of the New Perth Performing Arts Centre in a similarly busy locale”.
The first step he explains is to cast a post-tensioned ground floor slab on grade. As “top-down” suggests the basement levels were then excavated from around cast in situ belpiles that double as columns of the carpark, eventually suspending the slab. “Its similar to a mining operation” says Peter “As dirt is excavated beneath the slab there is no dust blowing around in the wind, and it can be loaded into trucks parked on the site instead of the street. At the same time construction can carry on in the upper part of the building. There are significant time savings with this construction approach – which the construction team estimated to be worth about ½ a million dollars”.
The belpile columns also doubled as a perimeter retention system linked by superfine injection grouting. The capacity of these piles was only sufficient for the suspended floor and the first floor so pad footings were tied into the belpile columns.
“The beauty of the system is that the ground floor slab provides environmental benefits, reducing dust off the site to just about nil and providing a surface for trucks to drive on with their deliveries” says Peter. Construction did not depend on closures of St Quentin’s Ave, which was the case for a neighbouring construction.
To avoid use of tower craneage the walls were constructed of a proprietary sandwich panel “AFS walls” composed of compressed fibre-cement panel filled with concrete in situ. Peter Airey is an enthusiast with regard to the product. “The process is very clean and results in excellent acoustic and thermal properties for residents near a busy highway. The finished panels have a high loadbearing capacity and were extensively used as shear walls and transfer beams. AFS walls doubling as transfer beams avoid the additional space enclosure that downstand beams would normally require” says Peter.
In the upper floors pre-stressed precast hollow core planks were specified for regular shaped areas and post-tensioned cast in situ concrete for areas with irregular shapes and where load transfer due to misalignment of walls can occur. The roof was conventional metaldeck supported on purlins which seat largely on AFS walls augmented with some conventional structural steel.
The result of the structural design? “We feel it contributes to the uncluttered architecture and is an industry showcase of concrete design and construct technique” says Peter. “The finished building showcases the architectural concept by John colliere of CMP Architects”.